SustainablE Steel Additive Manufacturing (SESAM)
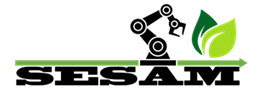
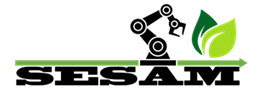
Why use additive manufacturing in steel production?
The manufacturing industry needs to become more sustainable, resilient, and innovative to maximise benefits for society and the economy, while lowering its environmental impact.
Additive Manufacturing is a promising technology with many possible benefits including:
- Speeding up product development.
- Increasing functionality of products.
- Reducing material waste.
- Raising industry resilience.
- Lowering environmental impact.
- Promoting the circular economy – by making it easy to replace and mend parts.
Integrating the SESAM-solution into existing production.
To secure and scale-up possible benefits for industry, key challenges include integrating additive manufacturing systems that are easy-to-use, simple to integrate in existing production flows and able to yield high-quality materials consistently.
The SustainablE Steel Additive Manufacturing (SESAM) project explores how to integrate a specific type of additive manufacturing, Laser-beam Directed Energy Deposition with wire (DED-LB/w), into steel production. By upscaling the use of the technology, the project team aims to show whether the technology can lower the climate impact of production, make large metallic structures simpler to build, and give rise to new business models.
Among approaches to additive manufacturing (AM), Laser-beam Directed Energy Deposition with wire (DED-LB/w) is a particularly promising pathway for next-generation industrial production.
The technology uses a high-power laser to melt metal wire into beads, which are deposited layer-by-layer into near-net shapes using an industrial robot arm.
This can significantly shorten the build time and allow for building large metallic structures.
Enabling broader use of DED-LB/w could make the procurement of large components in the manufacturing industry much simpler. This would help the industry, which is currently heavily dependent on a few global suppliers. Increasing the number of small suppliers can lead to sound competition and increased efficiency.
The SESAM project team wants to show whether DED-LB/w technology can be well-integrated into the existing supply chain. The project asks two key questions:
- Can this production method yield significant returns on investment?
- Can it reduce the environmental footprint of advanced manufacturing of high-end steel components?
THE SESAM SOLUTION
The SustainablE Steel Additive Manufacturing (SESAM) project seeks to show how Laser-beam Directed Energy Deposition with wire (DED-LB/w) can be brought into real production and well-integrated into the existing supply chain – and to investigate whether such a technology could yield significant returns on investment and reduce the environmental footprint of production.
Upscaling of DED-LB/w offers substantial economic potential, such as:
- Increasing the number of local suppliers of complex large-scale metallic structures.
- Increasing global competitiveness in laser-processing applications.
- Improving productivity, primarily by reducing defects and lowering reject rates of produced parts.
- Stimulating private investment in upscale DED-LB/w supply chain.
- Offering the possibility to create or safeguard more than 1,000 high-value jobs in Europe alone within the manufacturing, photonics and robotics industries.
- Providing indirect benefits, including more flexible, responsive, and custom-made manufacturing and repair of parts, with fewer delays, fewer defects, and faster delivery.
Webinar: The future of manufacturing: Integrating Sustainable Steel Additive Manufacturing into production
Join us for an engaging and informative session that will inspire new perspectives on the future of additive manufacturing! In this webinar, our experts from University West will share the challenges of finding the optimum process parameters to minimise defects and tailor microstructure and properties.
Key topics will be:
- The influence of wire feed rate on the presence of defects.
- The high deposition rate achieved with the process.
- The effectiveness of solution annealing in homogenising the microstructure and in dissolving intermetallics
- The energy savings when using AM 2205 wire vs conventional ER2209 wire.
What exactly is DED-LB/w?
The SESAM project is centred around Laser-beam Directed Energy Deposition with wire DED-LB/w AM technology that uses a high-power laser to melt metal wire into beads, which are deposited layer by layer into near-net shapes using an industrial robot arm.
This technology allows manufacturing of large metallic structures that re several meters in diameter, either by printing the entire structure, starting from a small substrate, or through hybrid fabrication that combines the use of sheet metal, welding and DED-LB/w together to create the final part.
Large metallic structures can be built within days or weeks, as compared to several months of lead time needed for traditional manufacturing routes.
Despite these benefits, the DED-LB/w process currently is used by only a few large players, mainly in the aerospace industry. This is mostly because manufacturers in this sector have historically large capacity and a tendency to favour in-house process development and qualification, as well as access to highly skilled operators. The automation system considered in this project is intended to lower the threshold for incorporating DED-LB/w into the existing supply chain, while allowing for its use in critical part production – by guaranteeing the defined process window, even in the face of process disturbances. The project includes a major effort for broad dissemination of results, with the help of EIT Manufacturing, because the partners are committed to ensuring wider implementation of DED-LB/w in Industry.
Enabling greater use of DED-LB/w can disrupt the manufacturing industry and its current procurement of large components, which in many cases are heavily dependent on a limited number of global suppliers. Increasing the number of local suppliers who can be contracted, for example providers of sheet metal and smaller forging work, can ensure sound competition and hence increased efficiency, and strengthened national economies. Overall transportation of goods would be reduced, as would material waste and usage of toxic chemicals needed for the excessive machining performed today.
What new business models are possible with DED-LB/w?
- New business models can include, for example, local “just-in-time factories”, that will be able to make complex parts or provide cost-effective repair for single high-value components.
- Local DED-LB/w capability provides fast availability of high-quality replacement parts, which help prevent costly downtime or the need for large inventories of critical spare parts.
- Customised high-integrity metal parts could be realised easily, and worn-out parts could even be repaired on site.
Expected results:
At the end of the project, a prototype additive manufacturing system, designed for production, will be in place at University West’s research facilities, Produktionstekniskt Centrum (PTC) in Trollhättan, Sweden. It will be integrated into a robotised laser welding cell, which represents a production-like setting. The project is intended to set up an additive manufacturing system that is able to build a multitude of geometries in a robust and automated fashion, with quality-assured, industry-level materials, reaching Technology readiness level (TRL) 7.
Why is this research important for society?
The broad-scale integration of additive manufacturing can speed product development, increase functionality of products, reduce material waste, raise industry resilience and lower environmental impact.
Can this technology reduce the climate impact of high-end steel components?
Sweden has one of the most ambitious goals for lowering CO2 emissions in the world. Transport and industry account for 30% of total emissions. Local production and higher efficiency in the use of energy and material can therefore be an impactful way to reduce overall environmental footprint.
A key potential outcome of the project is better sustainability.
Additive manufacturing is considered a “green technology” compared to most conventional manufacturing technologies, both due to waste reduction and lower energy consumption. Other important resource efficiency features of additive manufacturing are enabling remanufacturing and repair of parts. Additive manufacturing gives us a way to speed up the development of new, better materials and to manufacture materials that are currently difficult or impossible to manufacture. This will have a positive impact on the sustainability of products.
Among the project deliverables will be a white paper documenting methodology for life cycle inventory and assessing sustainable development.
The lead for this section of the project is Dr Claes Fredriksson, at the University West.
Project key facts
Name of project: SustainablE Steel Additive Manufacturing (SESAM)
- Project start: September 2022.
- Project length: 3 years.
- Technology Readiness Level: At start TRL 5, with some subsystems reaching TRL 6 – at the end of the project, TRL 7.
Project parties;
EIT Manufacturing’s role: EIT Manufacturing is responsible for dissemination of the project results as well as the work package on gender balance. EIT Manufacturing will play a significant role in spreading information about insights and results from the project, and to ensure that the project findings are useful for Europe’s manufacturing sector. This will include publishing the results through our website, increasing visibility through events and through learning paths on EIT Manufacturing platforms such as Skills.Move.
University West has more than 15 years of experience in additive manufacturing (AM). Its researchers have unique experience in solving automation issues for AM of advanced aero-engine materials using a robotised heat source for melting wire to build a pre-determined feature. Another enabler is that the SESAM project will be conducted in the research environment Production Technology West (PTW), which has extensive experience of running complex research projects in co-production with the industry.
Procada, is an SME specialised in automation and control solutions for DED-LB/w. Founded on experience gained from working with the technology since 2006 in the aerospace industry, Procada and its team provide innovation and industrialisation of DED-LB/w to customers.
ADAXIS is a French-Swedish robotics software startup developing software to make it effortless to turn industrial robotic arms into flexible 3D printers on demand. The company’s innovations are based on years of applied research into using industrial robotics for advanced manufacturing at RISE, Sweden and ESTIA, France. Its first product, AdaOne, was launched in early 2022 and supports 3D printing in metal, plastics, composites, and concrete.
Alfa Laval is a leading global provider of first-rate products in the areas of heat transfer, separation and fluid handling. With these as its base, Alfa Laval aims to help enhance the productivity and competitiveness of its customers in various industries throughout the world. We define their challenges and deliver sustainable products and solutions that meet their requirements – mainly in energy, the environment, food and the marine industry.
voestalpine Böhler Welding is a welding consumables and equipment manufacturing company. The firm is a leader in the welding industry with over 100 years of experience, more than 50 subsidiaries and more than 4,000 distribution partners around the world. Voestalpine Böhler Welding offers an extensive product portfolio and welding know-how combined with a global presence. Specifically for this project voestalpine Böhler Welding acts as provider of wire feedstock and the related expertise for its application in additive manufacturing.
Financing:
The project is co-funded by Vinnova Sweden’s innovation agency.
Project lead:
Robert Pederson, Professor, PhD
Department of Engineering Science, University West
The SESAM project team during a meeting in January 2023.