Success through networking
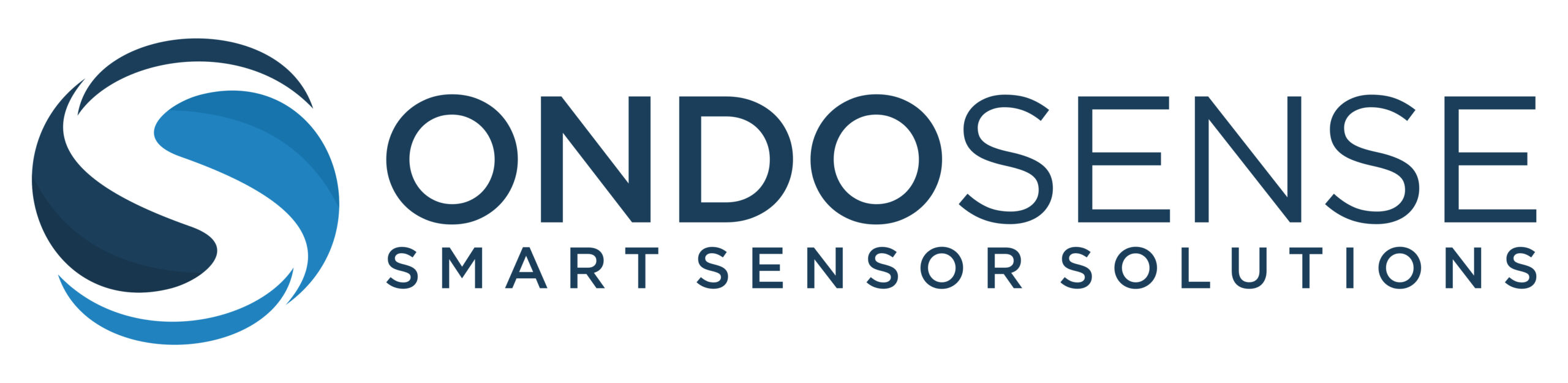
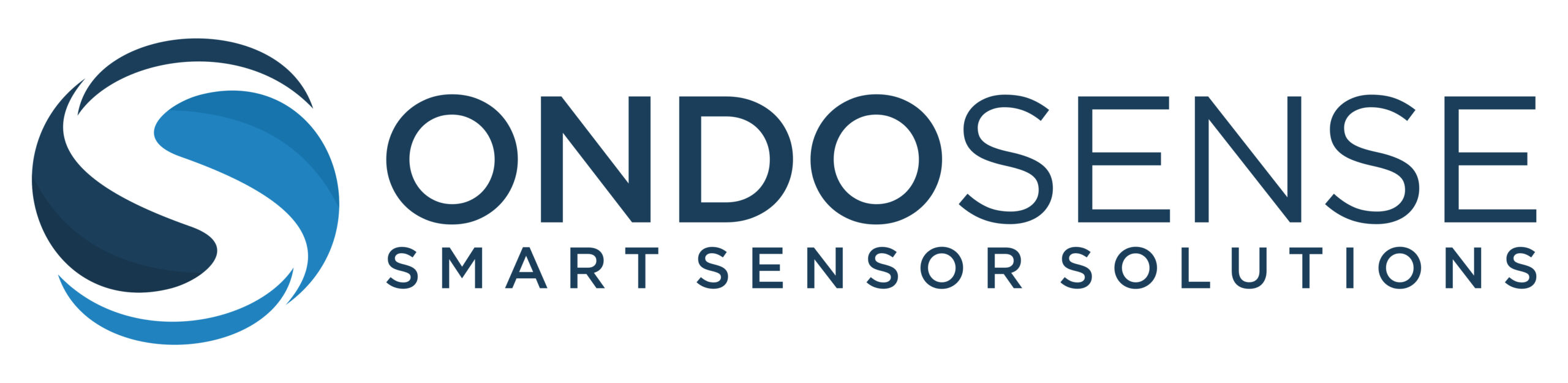
At the beginning of a success story there is something groundbreaking. In this case, a high-precision radar sensor that delivers accurate and reliable measurement results wherever conventional sensors fail.
With this innovation, three engineers succeeded in acquiring funding to spin off a company from the Fraunhofer Institute for Applied Solid State Physics in Freiburg. This is how the company OndoSense came into being in 2018. Its technology is now established on the market and in use in numerous industries. The company is also growing beyond Germany.
Innovation networks were important in the development of OndoSense, explains co-founder and CEO Dr Mathias Klenner: “We were active in the Baden-Württemberg network bwcon early on and have expanded our radius of action especially through EIT Manufacturing.” EIT Manufacturing is a Europe-wide network for all players from the manufacturing environment. According to Klenner, the financial support plays just as big a role as the contacts that are made through the networks. “Through these contacts, we had the opportunity to participate in a funded innovation project with partners with whom we would probably not otherwise have worked in this constellation.”
Intelligent work with collaborative robots
This project is about non-destructive quality control using collaborative robots. OndoSense adapts 3D radar sensors used in collision avoidance so that humans and machines can interact safely. The accuracy and reliability of the sensors ensures safe interaction, while the fact that they are radar sensors makes the solution privacy compliant. “Unlike camera-based systems, our sensors do not collect personal data – they only reliably register that someone is nearby, not who it is. We are now working on integrating the sensors into the kinematics of the robots,” says Klenner.
Safe human-machine collaboration
The background to the project are applications from the everyday testing routine of the High Performance Metals Division of the Austrian steel and technology group voestalpine: the usual testing with ultrasound takes time – scanning the components is time-consuming and highly repetitive for the skilled workers. By using quality control together with collaborative robots, skilled workers can focus their time on checking detected deviations and evaluating results – a win-win situation, as Philipp Horner, Chief Sustainability Officer High Performance Metals Division, points out. “The project is a great opportunity to make ideal use of the limited resources and expertise of our highly skilled professionals. They are relieved of routine activities and can thus use their expertise for detailed analysis of identified deviations.” The cooperation with the project partners works well, says Horner. “The composition fits. Our contacts at EIT Manufacturing have brought in the right people with the right approaches.”
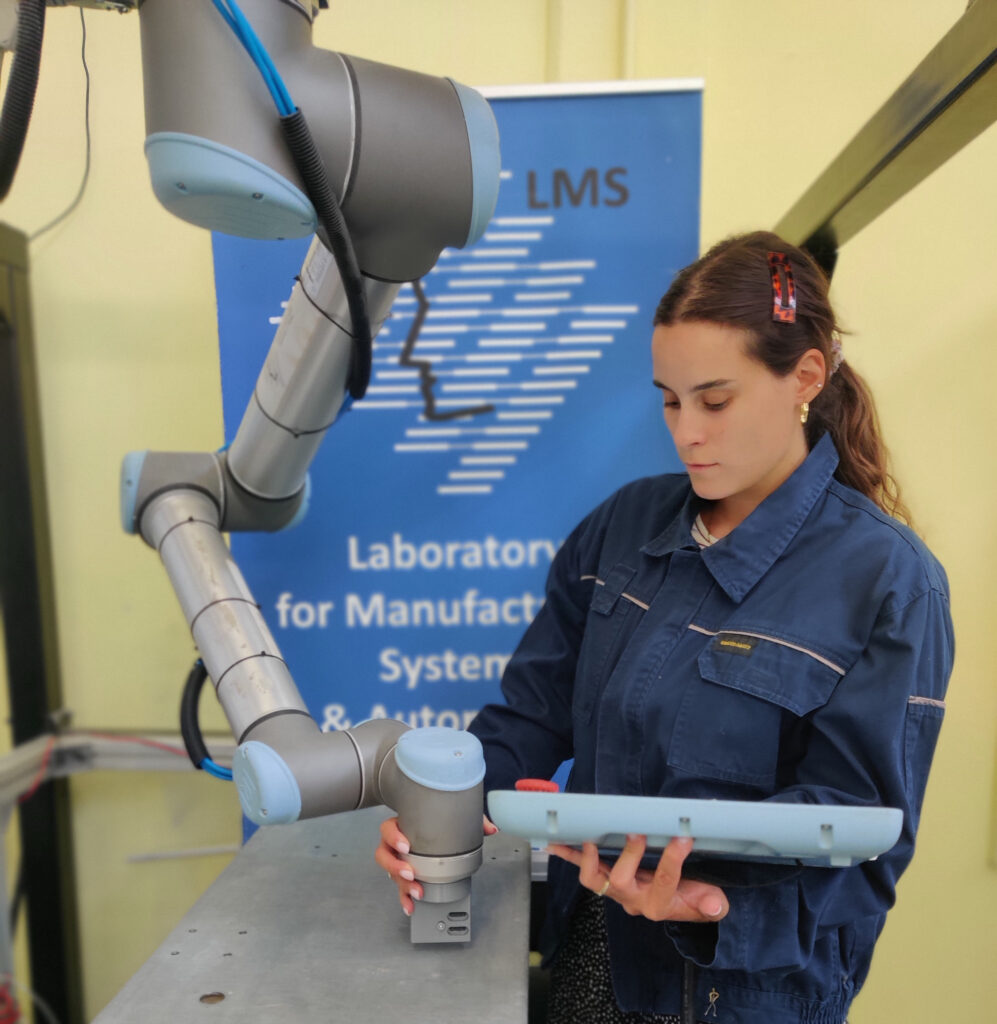
Pilot setup of the FlexbotNDT project, in which Awesome Technologies, Joanneum Research, LMS, OndoSense and voestalpine High Performance Metals are working on non-destructive quality control using collaborative robots.
Picture-book success story
For Dr Christian Bölling, managing director of the German branch of EIT Manufacturing, the career of OndoSense is an excellent example of how innovators can use networks to succeed. “Initial support and funding as well as new contacts came via competition entries in the Baden-Württemberg network bwcon. Our partners at bwcon pointed Mathias Klenner to our Start-up Competition 2020. We are happy to have contributed to the success story since then.”
Klenner won the 2020 competition by presenting network-enabled sensors that the OndoSense team had equipped with software to read and evaluate emerging data. “This solution has incredible potential because it is enormously versatile,” comments Wolfgang Kniejski, who builds and develops companies at EIT Manufacturing and has also supported OndoSense since 2020.
Opportunities for industry partners from the network
Kniejski recognised the opportunities for industrial partners of EIT Manufacturing: “The sensors can be used to measure workpieces, check fill levels, monitor wear, check materials or avoid collisions in production halls – and these are just some of the applications at our partners.” So he proposed a collaboration to OndoSense, a combination of coaching and joint appointments with a hand-picked clientele from different markets.
“Contacts are invaluable,” Bölling emphasises, “but especially for companies on an expansion course, access to money is just as important as access to markets.” During the COVID 19 pandemic, EIT Manufacturing supported OndoSense with money from a funding pot that enabled companies to close liquidity bottlenecks caused by the short-term withdrawal of customers and investors. In a 2021 financing round, OndoSense secured seven-figure growth financing and mezzanine financing granted by EIT Manufacturing was converted into equity.
Klenner assesses the financing round as a big step for the further development of the company. “This will allow us to grow much faster and thus leverage the enormous market potential that our technology has,” he comments, “not only in Germany, but internationally.”
This article first appeared in Produktion 15/2022 in German.